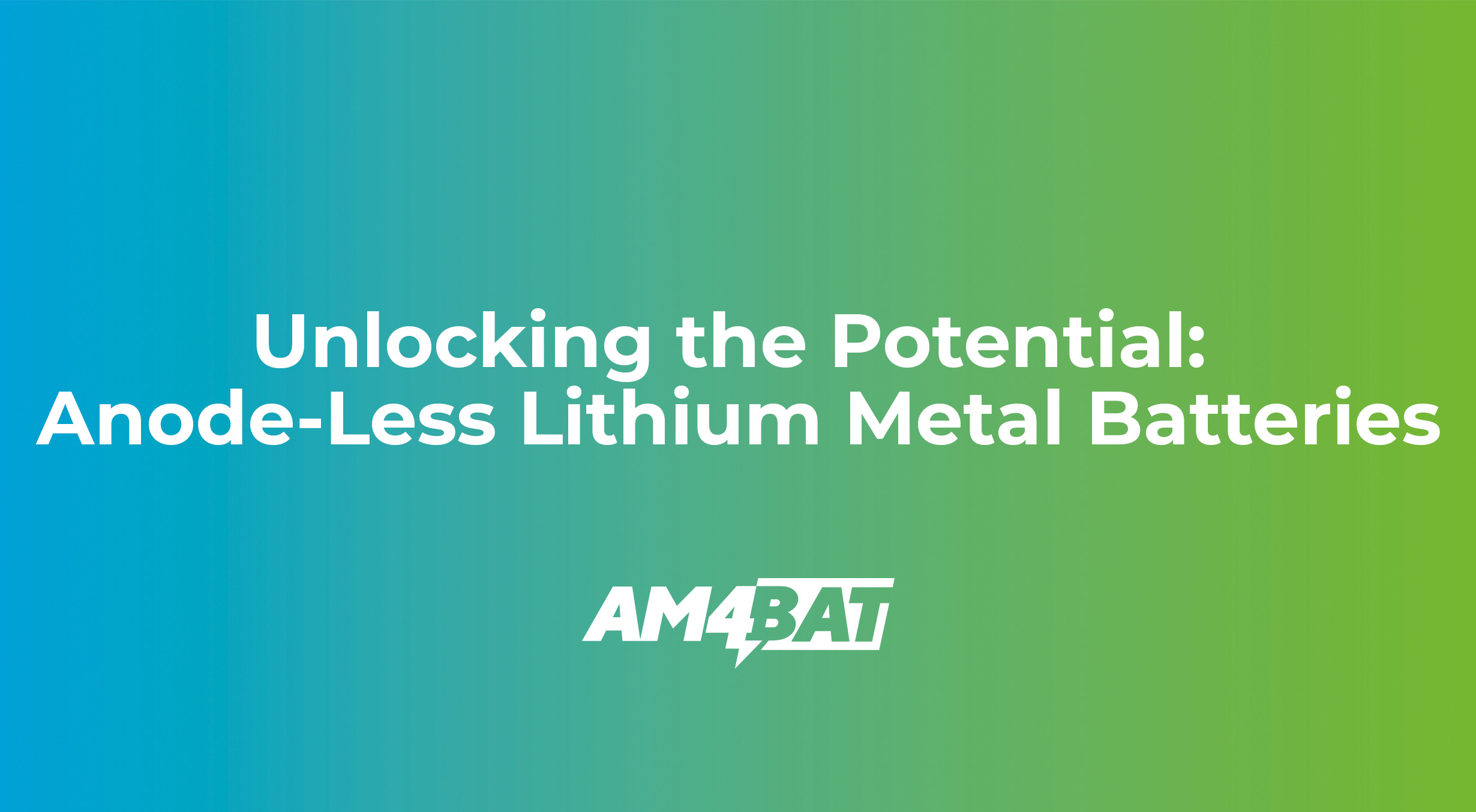
Unlocking the Potential: Anode-Less Lithium Metal Batteries
In today’s world, lithium-ion batteries have become an integral part of our daily lives, powering a diverse range of devices from smartphones to electric vehicles. As our reliance on these batteries grows, there’s an increasing demand for solutions that can pack more energy into them. This pursuit of improvement may lead to a fascinating development: the exploration of alternatives to the traditional graphite anode and one of the most promising candidates on the horizon is the anode-less lithium metal battery.
Understanding the Leap in Energy Density
To comprehend the concept of anode-less batteries and their necessity, let’s delve into what a lithium-metal battery is and understand its advantages and limitations. In the realm of Lithium-ion batteries, graphite has long been the go-to material for the anode. The theoretical volumetric capacity of graphite, a critical factor in determining battery’s energy density, stands at ~ 700 mAh/L. However, as we demand higher battery capacity, compromises like longer electrodes or increased loading in the coating process becomes necessary. Unfortunately, these compromises respectively lead to more inactive mass and a reduction in the battery’s power capability. Replacing graphite with Li metal, with its theoretical volumetric capacity of over 2000 mAh/L, can significantly boost energy density without the need for thicker or denser electrodes. But why isn’t this switch made if it’s so helpful?
Navigating challenges
While Li-metal batteries showcase immense potential, challenges persist. Issues like extensive solid-electrolyte interface (SEI) growth and the threat of dendrite lithium growth during battery operation pose safety risks. Due to Lithium’s high reactivity and consumption in each cycle, Li metal battery cell design often considers n/p ratios of 2 or more. This excess Li increases the likelihood of lithium dendrites formation and growth even more than expected. Manufacturing also faces hurdles due to the restricted environment required for lithium metal anode processing, contributing to higher production costs and challenges.
From left to right: A conventional Li-ion battery, A Lithium metal battery with excess Li, An Anode-less Li metal battery in fully charged state, and An anode-less Li metal battery in fully discharged state.
A Glimpse into the future: Anode-less Design
The innovative solution to these challenges lies in the concept of anode-less lithium metal batteries. But what does this mean in practice?
In anode-less configuration, there is no lithium metal, graphite, or in general any anode active material present during manufacturing. The process involves assembling the anode current collector along with other battery cell components during cell assembly, like the process for a conventional lithium-ion battery. The deposition of lithium on the anode current collector is expected to occur during the initial charge of the battery. Ideally, during discharge, all deposited lithium is stripped and returned to the cathode as its original and only source. Any residual lithium in the anode during discharge adversely impacts the battery’s coulombic efficiency and leads to capacity degradation with each cycle. In terms of safety, this battery addresses issues related to lithium-metal batteries by aiming for zero excess lithium meaning fewer chances for dendrite formation.
Engineering solutions The key to achieve this lies in the intricate interplay between the current collector, lithium ions, and electrolyte. Researchers worldwide are actively investigating solid-state electrolytes and current collectors tailored for anode-less lithium metal batteries. These efforts aim to overcome challenges associated with SEI growth and reversible stripping/plating, potentially unlocking a new era of high energy-density batteries. Anode-less lithium metal batteries present a paradigm shift in energy storage, offering a pathway to overcome the limitations of traditional lithium-ion batteries. As researchers explore innovative materials and manufacturing techniques, the outlook for a safer, more efficient, and cost-effective energy storage solution continues to brighten.